The global construction industry’s shift toward a plastics circular economy represents a transformative opportunity to reshape our approach to sustainable building practices. Each year, construction generates over 300 million tons of plastic waste, yet less than 10% gets recycled effectively. By reimagining plastics as a renewable resource rather than disposable material, forward-thinking construction professionals are pioneering closed-loop systems that capture significant economic and environmental value.
Recent technological advances in chemical recycling, coupled with innovative design principles, now enable construction companies to recover and repurpose up to 95% of plastic building materials. This systematic approach not only reduces waste and carbon emissions but also creates new revenue streams through material recovery and remanufacturing. Leading construction firms implementing circular plastics strategies report cost savings of 15-30% on material procurement while strengthening their competitive position in an increasingly sustainability-conscious market.
The transition to a plastics circular economy demands a fundamental shift in how we design, build, and manage construction projects. By adopting circular principles today, construction professionals can drive innovation, reduce environmental impact, and capture emerging opportunities in the rapidly evolving sustainable construction landscape. This article explores practical strategies for implementing circular plastics solutions across the construction value chain.
The Construction Industry’s Plastic Problem
Current Plastic Consumption Patterns
In modern construction, plastics have become integral to virtually every aspect of building projects, from structural components to finishing materials. Current consumption patterns show that approximately 20% of all plastic materials are utilized in construction, making it the second-largest consumer after packaging. Common applications include PVC pipes, electrical conduits, insulation materials, window frames, and synthetic flooring.
The industry’s reliance on virgin plastics is particularly evident in large-scale commercial projects, where materials like expanded polystyrene (EPS) and polyurethane foams are extensively used for insulation. Building envelope systems frequently incorporate plastic-based waterproofing membranes and vapor barriers, while interior finishes often feature acrylic-based paints and synthetic carpeting.
Recent data indicates that the average commercial building project generates approximately 30% of its waste from plastic materials during construction. Despite growing sustainability initiatives, less than 10% of construction plastics are currently recycled or repurposed, with the majority ending up in landfills. This consumption pattern presents both environmental challenges and opportunities for implementing circular economy principles in construction waste management.
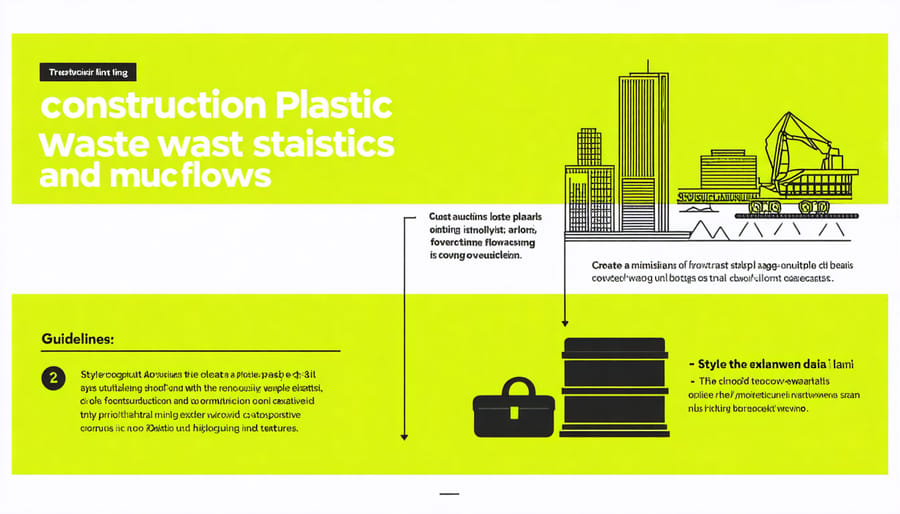
Environmental Impact Assessment
The environmental impact of construction plastic waste extends far beyond visible pollution, presenting significant challenges to ecosystems and climate systems. Recent studies indicate that construction-related plastic waste contributes approximately 23% of total plastic pollution, with much of this material persisting in the environment for centuries. The implementation of zero waste initiatives has revealed that improper disposal of construction plastics releases harmful chemicals into soil and groundwater, while incineration produces substantial greenhouse gas emissions.
Life cycle assessments demonstrate that traditional linear plastic use in construction generates 2.5 times more carbon emissions compared to circular approaches. Microplastic contamination from construction waste has been detected in marine ecosystems, affecting aquatic life and potentially entering the food chain. Furthermore, the degradation of construction plastics in landfills leads to the release of toxic additives, including phthalates and flame retardants, which pose risks to both environmental and human health. These findings underscore the urgent need for implementing circular economy principles in construction plastic management.
Implementing Circular Plastic Solutions
Design for Recyclability
Implementing effective design for recyclability strategies is crucial for advancing circular economy principles in construction. Architects and engineers must consider the entire lifecycle of plastic materials during the design phase to maximize recycling potential and minimize waste.
Key design strategies include utilizing mono-material solutions whenever possible, as mixed plastics are typically more challenging to recycle. For instance, specifying single-polymer window frames instead of composite materials significantly improves end-of-life recyclability. Additionally, designing for disassembly enables easier separation of different plastic components during demolition or renovation.
Material selection plays a vital role in recyclability. High-quality virgin plastics or recycled content that meets construction standards should be specified, with clear documentation of material composition. Mechanical connections should be favored over chemical bonds, allowing for straightforward separation during recycling processes.
Standardization of plastic components across projects can create economies of scale for recycling operations. This approach has proven successful in numerous European construction projects, where standardized PVC window profiles achieve recycling rates exceeding 80%.
Construction professionals should also consider incorporating visible material identification markers and establishing clear documentation systems for plastic components. This ensures that future demolition contractors can easily identify and sort materials for appropriate recycling streams, maximizing resource recovery and supporting long-term sustainability goals.
Recovery and Processing Systems
Modern recovery and processing systems for construction plastics utilize a combination of mechanical, chemical, and advanced sorting technologies to maximize material reclamation. Mechanical recycling remains the primary method, where plastics are sorted, shredded, cleaned, and reprocessed into pellets or flakes for remanufacturing. Advanced optical sorting systems equipped with near-infrared (NIR) technology can accurately identify and separate different plastic types, ensuring higher quality recycled materials.
Chemical recycling technologies, including pyrolysis and depolymerization, are gaining traction for handling complex or contaminated plastic waste. These processes break down plastics into their chemical building blocks, enabling the production of virgin-quality materials. This is particularly valuable for construction plastics that may contain additives or multiple polymer types.
Innovative processing systems now incorporate artificial intelligence and machine learning to optimize sorting efficiency and material identification. These smart systems can detect subtle variations in plastic composition and separate materials with unprecedented accuracy, reducing contamination in recycled outputs.
On-site processing units are emerging as a solution for large construction projects, allowing immediate material recovery and reducing transportation costs. These mobile units can process clean plastic waste directly at construction sites, creating a closed-loop system that supports immediate reuse or recycling of materials.
Quality control systems, including spectrometric analysis and melt flow testing, ensure recycled materials meet construction industry standards and specifications.
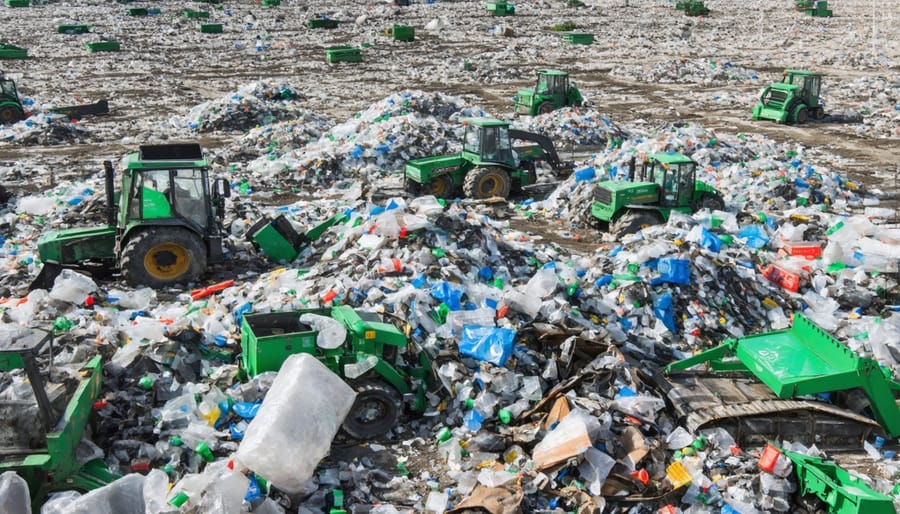
Reintegration into Supply Chains
The successful reintegration of recycled plastics into construction supply chains requires a systematic approach combining quality control, processing technology, and material standardization. Construction companies are increasingly adopting advanced sorting and processing techniques to ensure recycled plastics meet industry specifications for structural and non-structural applications.
Material Recovery Facilities (MRFs) play a crucial role by implementing multi-stage sorting processes, including Near-Infrared (NIR) spectroscopy and density separation, to produce high-quality recycled plastic pellets suitable for construction materials. These facilities work closely with manufacturers to develop standardized feedstock that meets specific performance requirements for different applications.
Leading construction companies are incorporating recycled plastics through various methods, including mechanical recycling for lower-grade applications and chemical recycling for high-performance materials. The integration process typically involves:
1. Quality assessment of recycled content
2. Blending with virgin materials in optimal ratios
3. Performance testing to ensure compliance with building codes
4. Certification of recycled content percentage
Recent innovations in compatibilizer technology have significantly improved the binding properties of mixed plastic waste, enabling higher incorporation rates in concrete additives, insulation materials, and composite building products. Companies are also establishing closed-loop supply chains, where construction waste is directly processed and returned as raw material for new projects, reducing dependency on virgin plastics while maintaining material quality and performance standards.
Case Studies: Circular Success Stories
Project Innovation Showcase
Several groundbreaking projects are demonstrating how successful circular economy implementations can revolutionize plastic usage in construction. The Netherlands’ PlasticRoad project stands out, having developed modular road sections made from recycled plastics that are both lightweight and durable. These innovative segments reduce installation time by 70% and have a projected lifespan triple that of traditional asphalt roads.
In Stockholm, the Circulus Project has pioneered a building facade system using recycled PET bottles transformed into architectural panels. The system not only diverts plastic waste from landfills but also provides superior thermal insulation properties, reducing energy consumption by up to 30%.
The Australian firm EcoBricks has developed a revolutionary construction block made from 95% recycled plastic waste, reinforced with innovative binding agents. These blocks are fire-resistant, waterproof, and offer excellent structural stability while being 60% lighter than traditional concrete blocks.
In Singapore, the PlasTech initiative has created a closed-loop system for construction site plastic waste, converting used packaging and protection materials into new construction products on-site. This approach has reduced plastic waste by 85% while decreasing material costs by 40%.
These projects demonstrate the vast potential of circular plastic solutions in construction, combining environmental responsibility with enhanced performance and cost efficiency.
Measurable Impact Results
Recent studies demonstrate significant quantifiable benefits from implementing circular plastic initiatives in construction. Projects implementing plastic recycling and reuse strategies have reported average waste reduction rates of 35-40%, translating to substantial cost savings and environmental benefits.
Analysis of circular plastic programs across major construction firms reveals a 25% decrease in virgin plastic procurement costs when incorporating recycled materials. Companies utilizing recycled plastic components in construction have documented energy savings of up to 80% compared to using virgin materials, while reducing carbon emissions by approximately 1.1-1.6 tons of CO2 per ton of recycled plastic used.
Financial metrics show compelling returns, with construction firms reporting average cost reductions of 15-20% in material expenses through plastic recycling programs. Extended producer responsibility (EPR) schemes have achieved collection rates exceeding 90% for specific plastic construction waste streams, while innovative sorting technologies have improved recycling efficiency by 40%.
Case studies from leading construction projects demonstrate that incorporating recycled plastic materials can achieve up to 30% weight reduction in certain building components while maintaining structural integrity. Additionally, circular plastic initiatives have created new revenue streams, with some companies reporting 10-15% increases in annual revenue through the sale of recycled materials and implementation of take-back programs.
These measurable impacts underscore the business case for adopting circular plastic strategies in construction, delivering both environmental and economic benefits.
Future Outlook and Industry Recommendations
Emerging Technologies
Several groundbreaking technologies are reshaping how the construction industry approaches plastic waste management and circularity. Advanced artificial intelligence and machine learning algorithms are now enabling automated sorting systems that can identify and separate different types of plastics with unprecedented accuracy, significantly improving recycling efficiency. These smart waste management solutions are particularly valuable for processing mixed construction waste streams.
Chemical recycling technologies, including pyrolysis and depolymerization, are gaining traction as they can break down complex plastic materials into their basic chemical components. This enables the production of virgin-quality recycled plastics, addressing previous quality limitations in mechanical recycling processes.
Blockchain technology is emerging as a crucial tool for tracking plastic materials throughout their lifecycle, ensuring transparency and accountability in the circular supply chain. This technology enables construction companies to verify the origin and composition of recycled materials, ensuring compliance with specifications and sustainability requirements.
Additive manufacturing (3D printing) with recycled plastics is showing promise for producing custom construction components while minimizing waste. New biodegradable alternatives and bio-based plastics are also being developed, incorporating natural fibers and renewable materials that maintain structural integrity while reducing environmental impact.
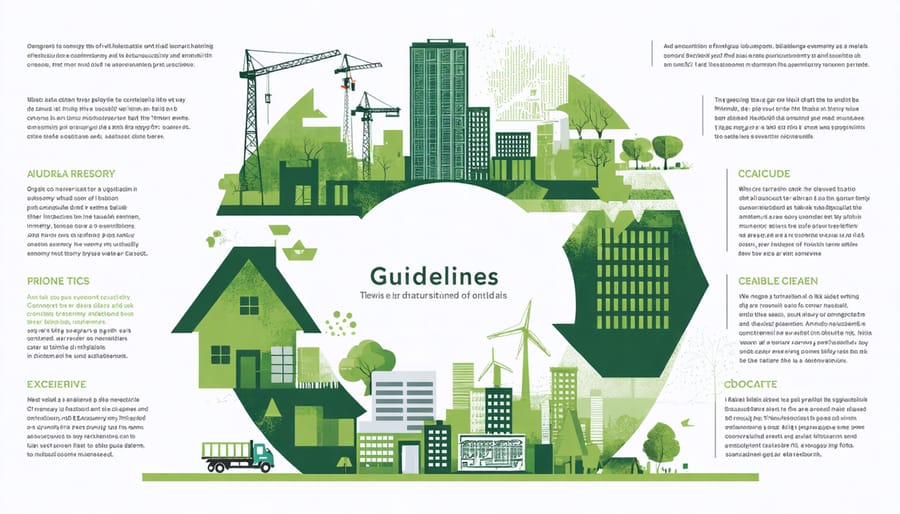
Implementation Roadmap
Successfully transitioning to circular plastic practices requires a structured, phased approach that considers both immediate and long-term objectives. Organizations should begin with a comprehensive audit of their current plastic usage and waste streams, identifying opportunities for reduction, reuse, and recycling.
Phase 1 (0-6 months) focuses on baseline assessment and goal setting. Companies should establish metrics for plastic consumption, conduct waste analysis, and identify key stakeholders. This phase includes setting realistic targets for plastic reduction and recycling rates while securing leadership buy-in.
Phase 2 (6-12 months) involves implementing initial changes. Organizations should introduce plastic segregation systems, establish relationships with recycling partners, and begin training staff on new procedures. Design teams should start incorporating circular principles into new projects, prioritizing recyclable and recycled plastic materials.
Phase 3 (12-24 months) centers on scaling and optimization. Companies should expand successful pilot programs, refine collection systems, and strengthen supplier partnerships. This phase includes implementing tracking systems for plastic usage and establishing closed-loop material flows where possible.
Phase 4 (24+ months) focuses on innovation and continuous improvement. Organizations should explore advanced recycling technologies, develop new applications for recycled materials, and collaborate with industry partners to address systemic challenges.
Throughout implementation, regular monitoring and reporting are essential to track progress and adjust strategies as needed. Success requires commitment from all organizational levels and effective communication with stakeholders, suppliers, and customers.
The transition to a plastics circular economy in construction represents both a critical challenge and an unprecedented opportunity for our industry. By implementing the strategies and best practices outlined above, construction professionals can significantly reduce waste, lower costs, and minimize environmental impact. The success of circular initiatives depends on collaborative effort across the supply chain, from manufacturers to contractors and waste management specialists. As industry leaders, we must prioritize sustainable material selection, implement robust recycling programs, and embrace innovative technologies that enable the reuse and recycling of plastic materials. The time to act is now – by adopting circular economy principles, we can create a more sustainable future for construction while maintaining profitability and performance standards. Let’s work together to transform how we use, reuse, and recycle plastics in construction, setting new benchmarks for environmental responsibility in our industry.