The construction industry stands at a pivotal crossroads where environmental responsibility meets technological innovation. Ecosmart construction, representing a paradigm shift in building methodology, combines cutting-edge sustainable materials with intelligent design principles to create structures that minimize environmental impact while maximizing operational efficiency. By integrating advanced building automation systems, renewable energy solutions, and bio-based materials, modern construction projects can reduce carbon emissions by up to 40% compared to traditional methods while delivering superior performance metrics.
As global construction spending approaches $12.9 trillion annually, the adoption of ecosmart practices has become not just an environmental imperative but a compelling business strategy. Leading construction firms implementing these technologies report an average 25% reduction in energy costs and a 30% decrease in water consumption, while achieving higher property valuations and meeting increasingly stringent environmental regulations.
This transformation in construction methodology represents more than just green building practices—it embodies a comprehensive approach to sustainable development that considers the entire lifecycle of a structure, from material sourcing to eventual demolition. For construction professionals and stakeholders, understanding and implementing ecosmart principles has become essential for maintaining competitive advantage in an increasingly environmentally conscious market.
Self-Healing Materials Transform Building Durability
Bacterial Concrete Technology
Bacterial concrete technology represents a groundbreaking advancement in self-healing building materials, utilizing microorganisms to enhance concrete durability and longevity. This innovative solution incorporates specifically selected bacterial spores, typically from the Bacillus family, which remain dormant within the concrete matrix until activated by crack formation.
When microcracks develop in the concrete structure, moisture penetration triggers the bacterial spores to germinate. These activated bacteria produce limestone (calcium carbonate) through a biochemical process, effectively sealing the cracks without human intervention. The bacterial healing mechanism can repair cracks up to 0.8mm wide, significantly extending the structure’s service life and reducing maintenance costs.
The incorporation of bacterial spores occurs during the concrete mixing process, where they are typically encapsulated in protective carriers such as clay pellets or gel-based systems. This encapsulation ensures the bacteria’s long-term survival within the harsh alkaline environment of concrete while maintaining their ability to activate when needed.
Field trials have demonstrated up to 40% reduction in maintenance costs for structures utilizing bacterial concrete, making it an increasingly attractive option for infrastructure projects requiring exceptional durability and reduced lifecycle costs.
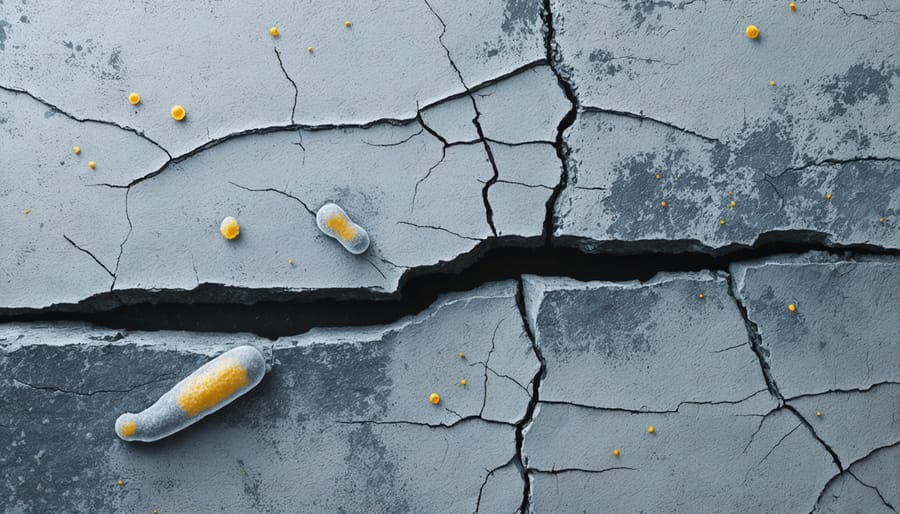
Shape Memory Materials
Shape memory materials represent a groundbreaking advancement in ecosmart construction, offering self-healing capabilities that significantly extend structural longevity. These innovative materials can return to their original form after experiencing deformation or damage, typically triggered by environmental stimuli such as temperature changes or electrical currents.
The most commonly used shape memory materials in construction include nickel-titanium alloys (Nitinol) and shape memory polymers (SMPs). Nitinol exhibits exceptional durability and can withstand repeated shape-recovery cycles, making it ideal for structural applications like self-tightening bolts and adaptive facade systems. SMPs offer greater design flexibility and lower production costs, finding applications in self-repairing concrete structures and smart insulation systems.
Recent implementations have demonstrated impressive results, with shape memory materials reducing maintenance costs by up to 30% in pilot projects. For instance, the integration of shape memory reinforcement bars in concrete structures has shown remarkable ability to close structural cracks automatically, preventing water infiltration and corrosion.
Despite higher initial costs, these materials provide substantial long-term value through reduced maintenance requirements and extended service life, aligning perfectly with sustainable construction principles. As manufacturing processes improve and costs decrease, shape memory materials are expected to become increasingly prevalent in ecosmart construction projects.
Energy-Active Building Components
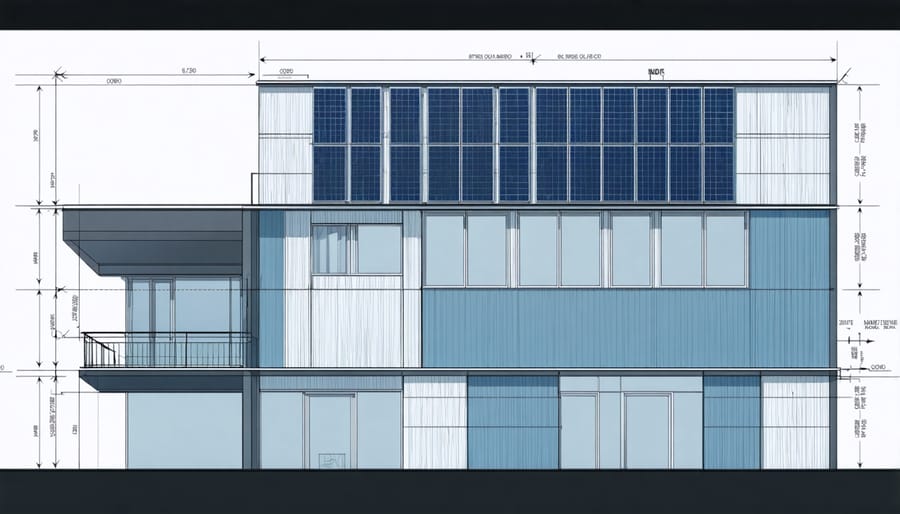
Photovoltaic Building Materials
Photovoltaic building materials represent a groundbreaking advancement in energy-efficient building solutions, seamlessly integrating solar power generation into the structural elements of buildings. These innovative materials include solar glass, photovoltaic roof tiles, and solar facade panels, which serve dual purposes as both construction components and power generators.
Solar glass technology has evolved significantly, offering varying degrees of transparency while maintaining power generation capabilities. This advancement allows architects to incorporate solar collection into windows and skylights without compromising natural light transmission or aesthetic appeal. Modern photovoltaic glass can achieve conversion efficiencies of up to 12%, while maintaining 50% transparency.
Photovoltaic roof tiles have revolutionized traditional roofing by replacing conventional materials with solar-active alternatives that mirror standard architectural styles. These tiles integrate seamlessly with non-solar roofing materials, offering superior weatherproofing while generating electricity. Recent technological improvements have increased their durability and power output, with some systems achieving 20% greater efficiency than traditional solar panels.
Solar facade panels represent the latest innovation in building-integrated photovoltaics (BIPV). These panels can be customized in various colors and textures, allowing architects to maintain design flexibility while incorporating renewable energy generation. Current market solutions offer power outputs ranging from 100-200 watts per square meter, depending on the installation angle and geographic location.
Phase Change Materials
Phase Change Materials (PCMs) represent a significant advancement in sustainable building technology, offering innovative solutions for thermal regulation in modern construction. These materials work by absorbing and releasing thermal energy during phase transitions, effectively maintaining consistent indoor temperatures while reducing HVAC energy consumption.
The most commonly used PCMs in construction include organic compounds like paraffin waxes and fatty acids, and inorganic materials such as salt hydrates. When integrated into building materials, PCMs can absorb excess heat during peak temperatures and release it when temperatures drop, creating a natural temperature regulation system.
Implementation methods include incorporating PCMs into wallboards, concrete mixtures, and insulation materials. For instance, PCM-enhanced drywall can store about five times more thermal energy than conventional drywall, significantly improving a building’s thermal performance. Recent developments have also introduced microencapsulated PCMs, which can be easily integrated into various construction materials without compromising their structural integrity.
Studies indicate that buildings utilizing PCM technology can reduce heating and cooling costs by 20-30% compared to conventional buildings. However, successful implementation requires careful consideration of factors such as the local climate, building usage patterns, and specific PCM melting points to maximize efficiency.
Industry experts recommend conducting detailed thermal analysis during the design phase to determine optimal PCM placement and quantity, ensuring the most cost-effective solution for each project.
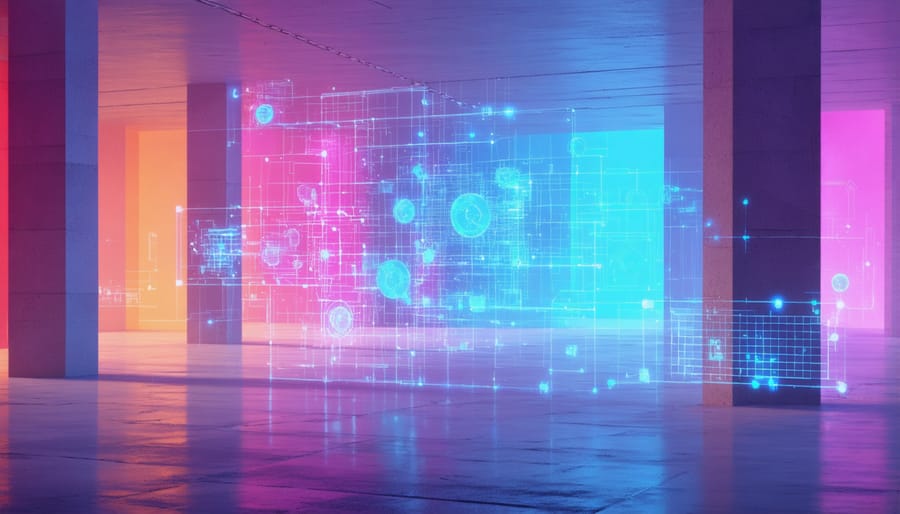
Smart Sensors and Responsive Materials
Structural Health Monitoring
Structural health monitoring represents a revolutionary advancement in ecosmart construction, employing sophisticated sensor networks and smart materials to continuously assess building integrity. These intelligent systems integrate seamlessly with smart building metrics to provide real-time data on structural performance, material fatigue, and potential vulnerabilities.
Advanced piezoelectric sensors and fiber optic systems embedded within structural elements monitor critical parameters such as strain, vibration, temperature, and moisture levels. This comprehensive monitoring network enables early detection of structural anomalies before they develop into significant problems, substantially reducing maintenance costs and extending building lifespans.
Recent implementations have demonstrated impressive results, with smart monitoring systems detecting minor structural changes up to 18 months before conventional inspection methods. The data collected through these systems feeds into predictive maintenance algorithms, enabling facility managers to optimize repair schedules and allocate resources more effectively.
Notable innovations include self-sensing concrete containing carbon nanotubes and graphene-based sensors that can detect microscopic cracks and stress concentrations. These technologies, combined with wireless sensor networks and cloud-based analytics platforms, create a robust framework for ensuring structural integrity while minimizing environmental impact through precise, targeted maintenance interventions.
Environmental Adaptation Systems
Environmental Adaptation Systems represent a breakthrough in sustainable construction, featuring materials and components that dynamically respond to changing environmental conditions. These innovative systems utilize smart technologies to optimize building performance and energy efficiency without manual intervention.
Key adaptative features include thermochromic glass that automatically adjusts its tint based on sunlight intensity, reducing cooling loads during peak hours. Shape-memory alloys in building facades respond to temperature fluctuations, automatically adjusting ventilation and solar gain. Advanced polymer composites in wall systems modify their thermal conductivity properties according to ambient conditions, enhancing insulation efficiency.
Living walls and bio-responsive materials integrate seamlessly with building management systems, responding to humidity, temperature, and air quality changes. Self-healing concrete containing specialized bacteria activates in response to moisture, automatically repairing micro-cracks before they become structural issues.
Recent developments include phase-change materials (PCMs) that absorb and release thermal energy based on temperature thresholds, providing passive temperature regulation. Smart windows with electrochromic coating respond to electrical signals, optimizing natural light and heat gain throughout the day.
These adaptive systems significantly reduce energy consumption while maintaining optimal indoor conditions, demonstrating the potential of responsive architecture in sustainable construction.
Cost-Benefit Analysis and Implementation
When evaluating ecosmart construction materials, a thorough cost-benefit analysis reveals both immediate expenses and long-term advantages. Initial implementation costs typically run 10-15% higher than traditional materials, primarily due to specialized manufacturing processes and limited market availability. However, studies indicate that these investments generally achieve ROI within 3-5 years through reduced energy consumption, lower maintenance requirements, and enhanced building performance.
Key financial considerations include material durability, energy efficiency gains, and potential tax incentives. Buildings incorporating ecosmart materials demonstrate average energy savings of 30-40% compared to conventional structures, significantly impacting operational costs. When analyzing sustainability metrics in construction, the long-term benefits often outweigh initial expenses.
Implementation strategies should focus on phased adoption, starting with high-impact areas like insulation, windows, and renewable energy systems. This approach allows organizations to manage costs while maximizing returns. Construction firms report success with pilot projects that demonstrate value before full-scale implementation.
Several factors influence successful implementation:
1. Supply chain optimization: Establishing relationships with reliable ecosmart material suppliers
2. Workforce training: Investing in proper installation techniques and handling procedures
3. Quality control: Implementing rigorous testing protocols to ensure material performance
4. Project scheduling: Accounting for potentially longer lead times on specialized materials
5. Regulatory compliance: Understanding and adhering to green building codes and certifications
Market analysis shows that buildings utilizing ecosmart materials command premium rental rates and higher resale values, typically 7-10% above market average. Additionally, these structures experience lower vacancy rates and attract environmentally conscious tenants, contributing to stronger long-term asset performance.
To optimize implementation, organizations should develop comprehensive transition plans that include detailed cost projections, performance metrics, and risk mitigation strategies. This ensures smooth integration while maintaining project timelines and budget constraints.
Real-World Applications and Case Studies
Several groundbreaking ecosmart construction projects have demonstrated the practical benefits and long-term value of sustainable building practices. The Bullitt Center in Seattle stands as a prime example of net-zero energy and water consumption, featuring advanced solar panels, geothermal wells, and composting toilets. Since its completion in 2013, the building has consistently exceeded its environmental performance targets while maintaining full occupancy.
In Europe, the Edge building in Amsterdam achieved the highest BREEAM sustainability score ever recorded. The building employs 28,000 sensors that monitor occupancy, movement, lighting levels, humidity, and temperature, creating an intelligent ecosystem that adjusts in real-time to optimize energy usage and occupant comfort. The structure uses 70% less electricity than typical office buildings.
The Vancouver Convention Centre West showcases large-scale green infrastructure integration with its six-acre living roof, seawater heating and cooling system, and on-site water treatment facility. The project has reduced water consumption by 60% compared to conventional buildings of similar size while supporting local biodiversity.
In Singapore, the Parkroyal Collection Pickering hotel demonstrates vertical greenery implementation at scale, with 15,000 square meters of sky gardens, reflecting pools, and cascading plantings. The design saves 32% in energy costs through passive cooling strategies and solar-powered systems.
The CopenHill waste-to-energy plant in Copenhagen represents innovative dual-purpose design, combining a power plant with public recreation space. The facility processes 400,000 tons of waste annually while featuring a green roof, hiking trail, and ski slope, proving that industrial facilities can contribute positively to urban environments.
These projects showcase how ecosmart construction principles can be successfully implemented across different building types and scales, delivering measurable environmental benefits while maintaining high standards of functionality and user experience. Their success has influenced building codes and sustainability standards worldwide, driving broader adoption of green building practices.
The future of ecosmart construction materials stands at a pivotal intersection of innovation, sustainability, and market demand. As global environmental standards become increasingly stringent, the construction industry is rapidly evolving toward materials that combine performance with ecological responsibility. Advanced composites, self-healing concrete, and bio-based materials are expected to dominate the next decade of construction innovation. Industry experts project that by 2030, ecosmart materials will constitute over 60% of new construction projects in developed markets. The integration of smart technology with sustainable materials will create building solutions that are not only environmentally conscious but also economically viable. This transformation represents more than a trend; it’s a fundamental shift in how we approach construction, promising a future where sustainability and structural integrity work in perfect harmony.