Energy optimization in modern construction demands a strategic fusion of advanced technology and proven energy-efficient building strategies. Building professionals now leverage real-time energy monitoring systems, capturing granular consumption data across HVAC, lighting, and operational systems to identify optimization opportunities that can reduce energy costs by 25-40%. Machine learning algorithms continuously analyze building performance metrics, automatically adjusting systems based on occupancy patterns, weather conditions, and peak demand periods.
The integration of smart building envelopes – incorporating dynamic glazing, advanced insulation materials, and adaptive façade systems – creates an intelligent thermal barrier that responds to environmental changes, minimizing energy loss while maintaining optimal indoor conditions. This approach, combined with renewable energy systems and energy storage solutions, establishes a comprehensive framework for achieving net-zero energy performance in commercial and residential projects.
Industry data demonstrates that properly implemented energy optimization protocols deliver ROI within 2-5 years, while reducing operational costs by up to 30% annually. These benefits extend beyond immediate energy savings, encompassing improved building resilience, enhanced occupant comfort, and significant reductions in carbon emissions – critical factors in meeting increasingly stringent building codes and sustainability requirements.
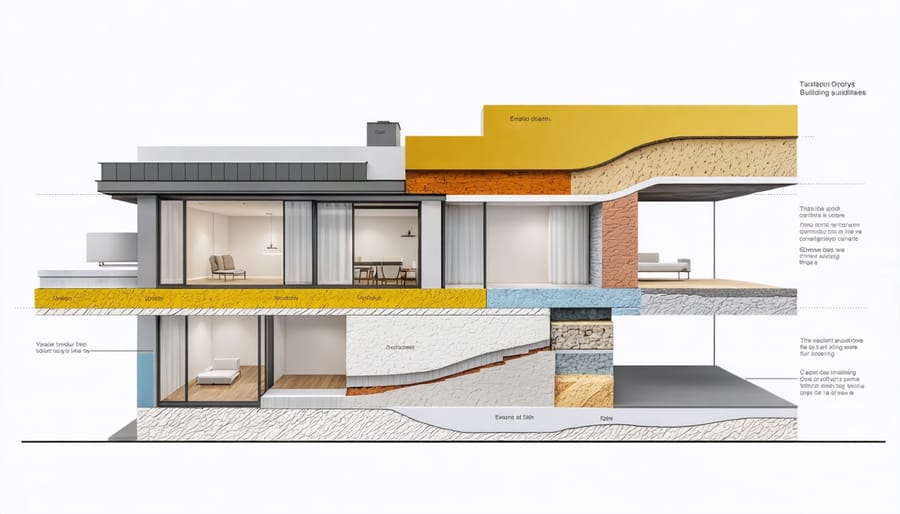
Building Envelope Optimization
Advanced Insulation Technologies
Modern insulation technologies have revolutionized building energy efficiency through innovative materials and application methods. Aerogel-based insulation, with its remarkably low thermal conductivity of 0.015 W/mK, leads the market in high-performance solutions. This ultra-light material, derived from silica gel, provides superior thermal resistance while requiring minimal installation thickness.
Vacuum Insulated Panels (VIPs) represent another breakthrough, offering R-values up to R-60 per inch, approximately ten times more effective than traditional fiberglass insulation. While their initial cost is higher, VIPs are particularly valuable in space-constrained retrofit projects where maximum thermal performance is essential.
Phase Change Materials (PCMs) have emerged as dynamic insulation solutions, actively managing heat flow by changing their physical state. These materials can absorb, store, and release thermal energy, effectively regulating indoor temperatures and reducing HVAC loads by up to 25%.
Advanced spray foam systems now incorporate graphene and carbon nanotubes, enhancing their thermal resistance and structural properties. These next-generation foams provide superior air sealing while improving the overall building envelope performance. Installation techniques have also evolved, with precision application equipment ensuring consistent coverage and optimal thermal bridging prevention.
Biomaterial-based insulation products, such as mycelium composites and processed agricultural waste, offer sustainable alternatives with comparable performance to conventional materials. These solutions typically achieve R-values between R-3.6 and R-3.8 per inch while significantly reducing embodied carbon.
The integration of smart sensors with modern insulation systems enables real-time monitoring of thermal performance and moisture levels, allowing facility managers to optimize building performance continuously and prevent potential degradation issues proactively.
High-Performance Windows and Doors
High-performance windows and doors represent a critical component in achieving optimal energy efficiency in modern buildings. These fenestration solutions can reduce heating and cooling costs by 25-30% compared to standard options while enhancing occupant comfort and building aesthetics.
Key performance metrics include U-factor, Solar Heat Gain Coefficient (SHGC), and Air Leakage ratings. Advanced double-pane and triple-pane windows with low-emissivity (low-E) coatings and argon or krypton gas fills achieve U-factors as low as 0.20, significantly outperforming traditional single-pane alternatives that typically rate at 1.0 or higher.
Frame materials play a crucial role in thermal performance. While aluminum frames are durable, they require thermal breaks to prevent heat transfer. Composite frames, incorporating materials like fiberglass or vinyl, offer superior insulation properties while maintaining structural integrity. Recent innovations include warm-edge spacer technology and dynamic glazing systems that adjust tint levels based on external conditions.
For commercial applications, curtain wall systems with integrated thermal barriers and pressure-equalized rain screens have become industry standard. These systems not only optimize energy performance but also enhance building envelope integrity.
Installation quality significantly impacts performance. Proper air sealing, flashing, and integration with the building envelope are essential. According to recent field studies, improper installation can reduce energy efficiency by up to 50%, highlighting the importance of certified professionals and rigorous quality control measures.
When selecting high-performance windows and doors, professionals should consider climate zone requirements, building orientation, and specific application needs while ensuring compliance with local energy codes and standards.
Smart HVAC Systems Integration
AI-Powered Climate Control
Artificial intelligence is revolutionizing the way buildings manage their climate control systems, offering unprecedented levels of efficiency and comfort. By integrating modern HVAC technologies with machine learning algorithms, buildings can now anticipate and adapt to changing conditions in real-time.
These intelligent systems analyze multiple data points, including occupancy patterns, weather forecasts, thermal loads, and historical performance metrics, to optimize HVAC operations. The implementation of AI-powered energy optimization has demonstrated energy savings of 20-30% in commercial buildings while maintaining or improving occupant comfort.
Recent case studies from major commercial developments showcase the practical benefits. The Capital Tower in Singapore implemented AI-driven HVAC controls in 2022, resulting in a 25% reduction in cooling costs within the first year. The system’s predictive maintenance capabilities also reduced unexpected downtime by 40%, significantly improving operational efficiency.
The technology operates through a network of IoT sensors that continuously monitor environmental conditions. Machine learning algorithms process this data to create dynamic thermal models of the building, enabling precise control of heating and cooling zones. This granular approach eliminates the energy waste associated with traditional fixed-schedule systems.
Furthermore, AI systems can integrate with building automation platforms to orchestrate multiple building systems simultaneously. For instance, smart algorithms can coordinate natural ventilation, solar gain, and mechanical cooling to maintain optimal conditions while minimizing energy consumption. The system’s ability to learn and adapt means it becomes more efficient over time, continuously refining its control strategies based on actual performance data.
For construction professionals considering implementation, the initial investment typically shows returns within 18-24 months through reduced energy costs and maintenance expenses. The key to successful deployment lies in proper system commissioning and integration with existing building management systems.
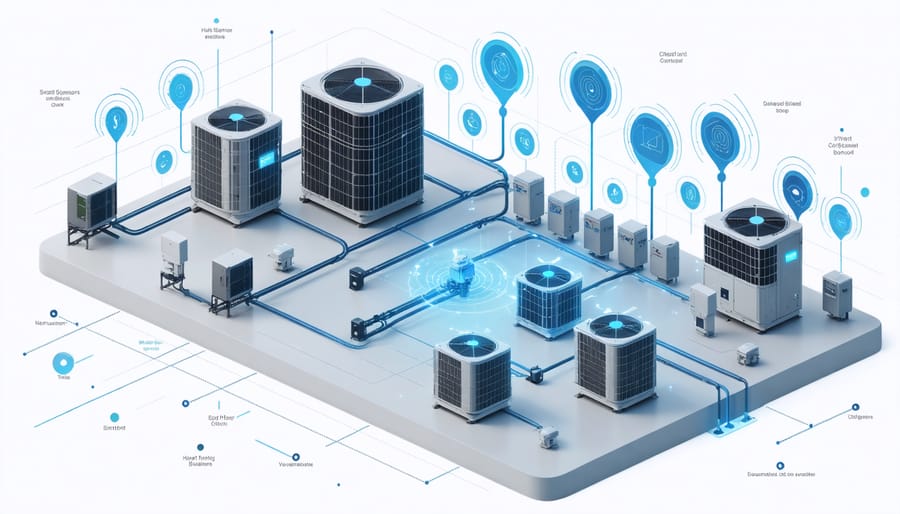
Heat Recovery Systems
Heat recovery systems represent a crucial component in modern energy optimization strategies, offering significant potential for reducing energy consumption and operating costs in buildings. These systems capture and repurpose waste heat from various processes, effectively maximizing energy efficiency across the facility.
At the core of heat recovery technology is the Heat Recovery Ventilation (HRV) system, which transfers heat from exhaust air to incoming fresh air during the winter months, while the process reverses in summer. This technology typically achieves efficiency rates of 75-85%, substantially reducing the energy required for heating and cooling.
Industrial applications often implement plate heat exchangers and rotary thermal wheels, which can recover up to 85% of waste heat from manufacturing processes. These systems are particularly effective in facilities with high-temperature operations, such as data centers, manufacturing plants, and commercial kitchens.
Recent innovations in heat recovery technology include advanced heat pumps that can capture low-grade waste heat and upgrade it to useful temperatures. According to industry studies, implementing comprehensive heat recovery systems can reduce heating costs by 20-40% in commercial buildings.
Case Study: A manufacturing facility in Michigan implemented a heat recovery system that captures waste heat from compressors and production equipment. The system generates annual energy savings of $175,000 while reducing CO2 emissions by 850 metric tons.
Key considerations for implementing heat recovery systems include:
– Initial system cost versus projected energy savings
– Available waste heat sources and their temperature levels
– Space requirements for equipment installation
– Maintenance needs and operational complexity
– Integration with existing HVAC systems
For optimal results, heat recovery systems should be incorporated during the initial design phase, though retrofit solutions are also available. Regular maintenance and monitoring ensure sustained performance and maximize return on investment. Professional energy audits can help identify the most suitable heat recovery opportunities for specific facilities.
Renewable Energy Integration
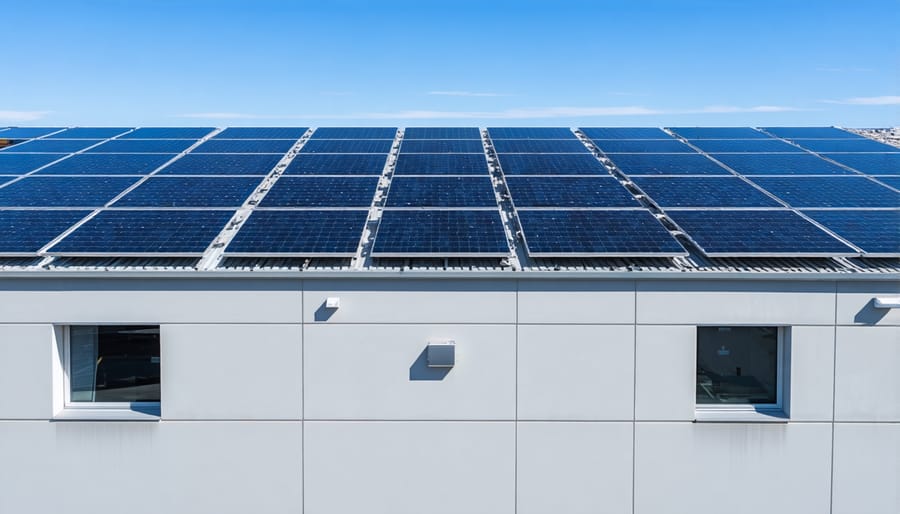
Solar-Ready Design
Incorporating solar readiness into building design has become a crucial consideration for modern construction projects. The key to successful solar integration lies in early planning and strategic design decisions that facilitate future solar panel installation while maximizing potential energy generation.
Building orientation plays a fundamental role in solar readiness. Structures should be designed with roof surfaces facing within 30 degrees of true south, ensuring optimal sun exposure throughout the day. The roof structure must be engineered to support both the dead load of solar panels (typically 3-6 pounds per square foot) and additional live loads from wind and snow.
Essential infrastructure preparations include installing electrical conduit runs from the roof to the main electrical room, reserving wall space for inverters and monitoring equipment, and designating a location for the main service panel. These pre-installed pathways significantly reduce future installation costs and minimize disruption during solar system deployment.
Roof design considerations should include minimizing obstructions such as vents, chimneys, and HVAC equipment on south-facing surfaces. Implementing a consolidated mechanical zone on the north side of the roof preserves valuable solar space. The roof material and warranty should also be compatible with solar installation, with a service life matching or exceeding the expected 25-30 year lifespan of solar panels.
Documentation of solar-ready features should be included in building plans, specifying reserved roof areas, structural capacity, and electrical infrastructure to facilitate seamless future integration of solar technology.
Energy Storage Solutions
Modern construction projects increasingly rely on advanced building energy storage solutions to maximize efficiency and reduce operational costs. Battery Energy Storage Systems (BESS) have emerged as a cornerstone technology, enabling buildings to store excess energy during off-peak periods and deploy it during high-demand times.
Lithium-ion batteries remain the predominant choice for commercial applications, offering high energy density and declining installation costs. However, emerging technologies like flow batteries show promise for larger-scale applications, providing longer discharge durations and reduced degradation over time.
Thermal energy storage systems, including phase change materials and ice storage, complement electrical storage solutions by managing heating and cooling loads more effectively. These systems can reduce HVAC energy consumption by up to 35% in commercial buildings.
Integration with building management systems (BMS) enables sophisticated control strategies, allowing facilities to optimize energy usage patterns and participate in demand response programs. Smart controllers can automatically determine whether to store or discharge energy based on real-time pricing and demand signals.
Recent case studies demonstrate that properly sized storage systems can achieve ROI within 5-7 years through peak demand reduction, energy arbitrage, and enhanced grid reliability. For maximum benefit, storage solutions should be designed in conjunction with on-site renewable energy systems and configured to support specific building load profiles.
Building Management Systems
IoT Sensors and Monitoring
IoT sensors and monitoring systems have revolutionized energy management in modern construction projects, enabling real-time tracking and optimization of energy consumption patterns. These smart devices form an interconnected network that continuously collects, analyzes, and reports critical data points throughout the building ecosystem.
Key sensor implementations include occupancy detectors, temperature monitors, lighting level sensors, and power consumption meters. These devices work in concert to create a comprehensive energy monitoring infrastructure that enables precise control over building systems. For instance, occupancy sensors can automatically adjust HVAC settings based on room usage patterns, potentially reducing energy waste by 15-30%.
Advanced IoT platforms integrate these sensors with building management systems (BMS) to enable automated responses and predictive maintenance. Real-time data analytics help identify energy consumption anomalies, equipment inefficiencies, and opportunities for optimization. Studies show that IoT-enabled buildings typically achieve 20-25% reduction in energy costs compared to conventional structures.
Implementation considerations include sensor placement optimization, network infrastructure requirements, and data security protocols. Strategic positioning of sensors ensures comprehensive coverage while minimizing hardware costs. Industry best practices recommend installing sensors at key consumption points and high-traffic areas for maximum effectiveness.
Data collected through IoT sensors also facilitates energy performance benchmarking and compliance reporting. Modern sensors can track multiple parameters simultaneously, including temperature, humidity, CO2 levels, and power quality, providing a holistic view of building performance. This granular monitoring enables facility managers to make data-driven decisions about energy optimization strategies and validate their effectiveness through quantifiable metrics.
Regular calibration and maintenance of these sensors ensure accurate readings and reliable performance, making them an invaluable tool in achieving sustainable energy management goals.
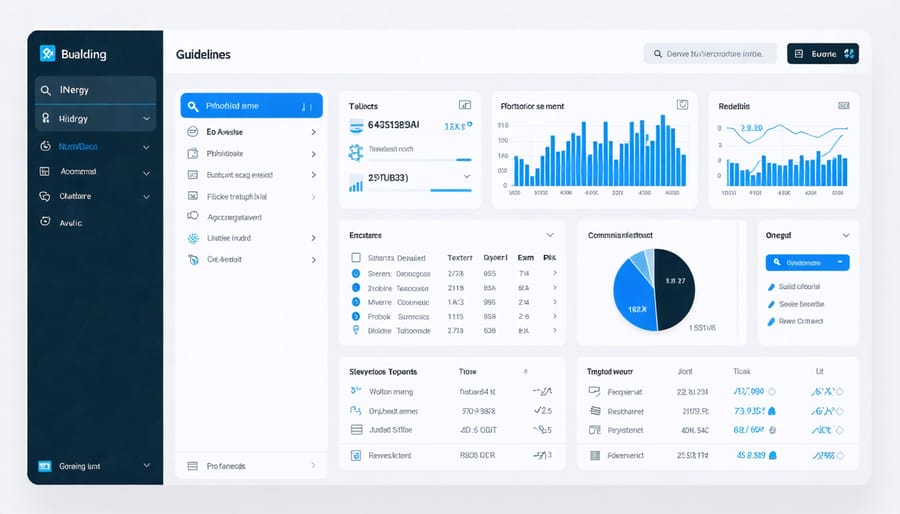
Predictive Maintenance
Predictive maintenance represents a paradigm shift in energy optimization, leveraging advanced data analytics and IoT sensors to anticipate and prevent system inefficiencies before they impact performance. By continuously monitoring key performance indicators (KPIs) such as temperature, vibration, power consumption, and operational patterns, facility managers can identify potential issues early and optimize maintenance schedules.
Modern building management systems (BMS) utilize machine learning algorithms to analyze historical performance data and establish baseline operational parameters. These systems can detect subtle deviations that might indicate developing problems, such as failing HVAC components or degrading insulation performance. For example, a study conducted across commercial buildings in Singapore demonstrated that predictive maintenance reduced energy waste by 15-20% compared to traditional maintenance approaches.
The implementation of predictive maintenance strategies typically involves:
– Real-time monitoring of equipment performance metrics
– Advanced analytics to identify patterns and anomalies
– Automated alerts for potential system failures
– Data-driven maintenance scheduling
– Performance optimization recommendations
Case studies from major commercial developments show that predictive maintenance not only reduces energy consumption but also extends equipment lifespan by 20-30%. The initial investment in sensor technology and analytics platforms typically achieves ROI within 12-18 months through reduced maintenance costs and improved energy efficiency.
For optimal results, facility managers should integrate predictive maintenance data with other building systems and establish clear performance benchmarks. Regular calibration of sensors and continuous refinement of predictive models ensure the system maintains its effectiveness over time.
Energy optimization in construction continues to evolve as a critical factor in sustainable building development. The strategies discussed throughout this article demonstrate the industry’s commitment to reducing energy consumption while maximizing operational efficiency. By implementing advanced building automation systems, incorporating renewable energy solutions, and utilizing smart materials, construction professionals can achieve significant energy savings and enhanced building performance.
The data from numerous case studies shows that integrated approaches to energy optimization can yield energy savings of 30-50% compared to conventional building methods. The combination of passive design strategies, active systems optimization, and regular maintenance protocols creates a comprehensive framework for sustainable energy management.
Looking ahead, the construction industry is poised for further advancement in energy optimization technologies. Emerging trends include artificial intelligence-driven building management systems, advanced energy storage solutions, and innovative materials with superior thermal properties. The integration of Internet of Things (IoT) devices and real-time energy monitoring systems will enable more precise control and optimization of building energy consumption.
For construction professionals, staying informed about these developments and maintaining flexibility in adoption strategies will be crucial. The future success of energy optimization initiatives will depend on the industry’s ability to balance initial implementation costs with long-term operational benefits.
As regulations become more stringent and environmental concerns more pressing, energy optimization will remain at the forefront of construction innovation. Construction professionals who embrace these technologies and strategies now will be better positioned to meet future challenges and deliver increasingly efficient building solutions that benefit both clients and the environment.