Electronic inventory management revolutionizes construction operations by delivering real-time visibility, reduced waste, and automated procurement processes across multiple job sites. Industry leaders leveraging IoT-enabled systems report up to 35% reduction in carrying costs and 40% fewer stockouts, with real-world IoT implementation results demonstrating significant ROI within the first year of deployment.
Advanced RFID sensors, cloud-based tracking platforms, and predictive analytics now enable construction firms to maintain optimal stock levels, forecast material requirements with precision, and eliminate costly delays that traditionally plague project timelines. This technological transformation addresses the construction industry’s persistent challenges of material waste, theft prevention, and supply chain disruptions while providing unprecedented control over inventory investments.
For project managers and construction executives seeking competitive advantages, electronic inventory management represents a critical stepping stone toward digital maturity. By integrating these systems with existing enterprise software, organizations can create a seamless flow of data that supports informed decision-making and proactive resource allocation across their entire project portfolio.
The Evolution of Electronic Inventory Management in Construction
Traditional vs. Electronic Systems
Traditional inventory management in construction relied heavily on manual processes, including paper-based tracking systems, physical counts, and spreadsheet documentation. These methods, while familiar, often led to errors, delays, and significant resource allocation for basic tracking tasks. The shift to modern digital procurement systems has transformed how construction companies handle their inventory workflows.
Electronic systems offer real-time visibility, automated reordering capabilities, and precise tracking through barcode scanning or RFID technology. Unlike traditional methods that require manual data entry and reconciliation, electronic solutions automatically update inventory levels, generate reports, and alert managers when stock reaches predetermined thresholds. This automation significantly reduces human error and the time spent on inventory-related tasks.
The contrast in efficiency is particularly evident in large-scale projects, where traditional systems struggled with multi-site inventory coordination. Electronic management solutions enable seamless integration across multiple locations, providing instant updates and accurate stock levels across the entire operation, while traditional methods often resulted in communication delays and coordination challenges between sites.
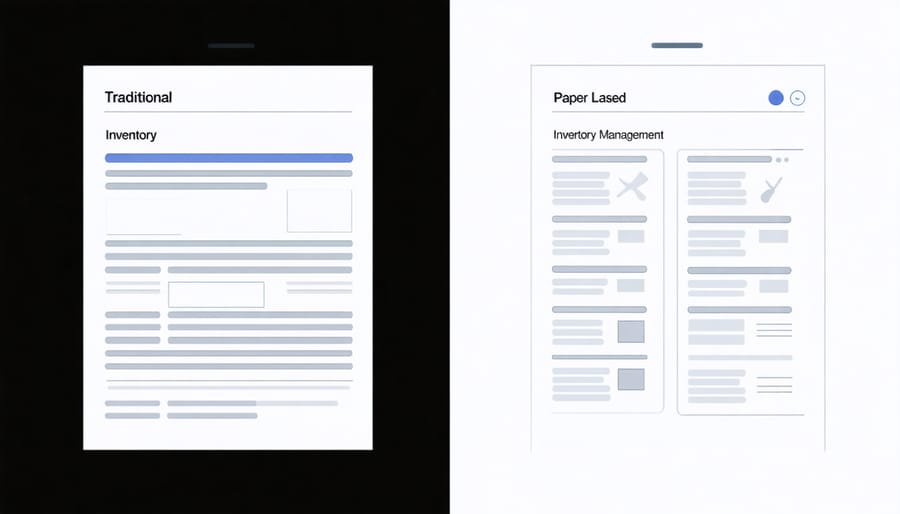
Key Components of IoT Inventory Solutions
IoT-enabled inventory management systems rely on several interconnected components that work together to create a comprehensive tracking and monitoring solution. At the core are IoT sensors and RFID tags, which attach to materials, equipment, and tools to provide real-time location and status updates. These sensors communicate with strategically placed gateway devices that collect and transmit data to cloud-based servers.
Data processing units serve as the system’s brain, analyzing incoming information and generating actionable insights. They utilize advanced algorithms to monitor stock levels, predict maintenance needs, and optimize inventory allocation across multiple construction sites.
Mobile applications and web-based dashboards provide user interfaces for accessing inventory data, generating reports, and managing alerts. These interfaces enable construction managers to track assets remotely and make informed decisions about resource allocation.
Integration middleware ensures seamless communication between IoT devices and existing enterprise systems, including procurement software and project management tools. Additionally, robust security protocols protect sensitive inventory data through encryption and access controls, while edge computing capabilities enable faster processing of time-critical information at the construction site level.
Real-Time Tracking and Monitoring Capabilities
RFID and Sensor Integration
RFID (Radio-Frequency Identification) technology and sensor integration represent a significant advancement in electronic inventory management for construction projects. These systems provide real-time tracking and monitoring capabilities that dramatically improve inventory accuracy and control.
Modern RFID systems utilize passive or active tags attached to materials, equipment, and tools. Passive tags, which are more cost-effective, work well for tracking bulk materials and smaller tools, while active tags, with their extended range and battery power, are ideal for high-value equipment and vehicles. Strategic placement of RFID readers throughout storage areas and job sites creates a comprehensive tracking network that automatically records movement and location data.
Integration with environmental sensors adds another layer of inventory management capability. Temperature sensors monitor climate-sensitive materials, while humidity sensors protect moisture-vulnerable items. Motion and pressure sensors detect unauthorized movement and help prevent theft, while proximity sensors assist in maintaining proper storage spacing and organization.
The combined system feeds data into a central management platform, enabling:
– Automatic inventory updates
– Real-time location tracking
– Environmental condition monitoring
– Theft prevention alerts
– Usage pattern analysis
– Maintenance scheduling
Recent implementations in large-scale construction projects have demonstrated up to 95% reduction in inventory counting time and a 30% decrease in lost or misplaced items. These improvements translate directly into reduced operational costs and increased project efficiency, making RFID and sensor integration a valuable investment for construction operations.
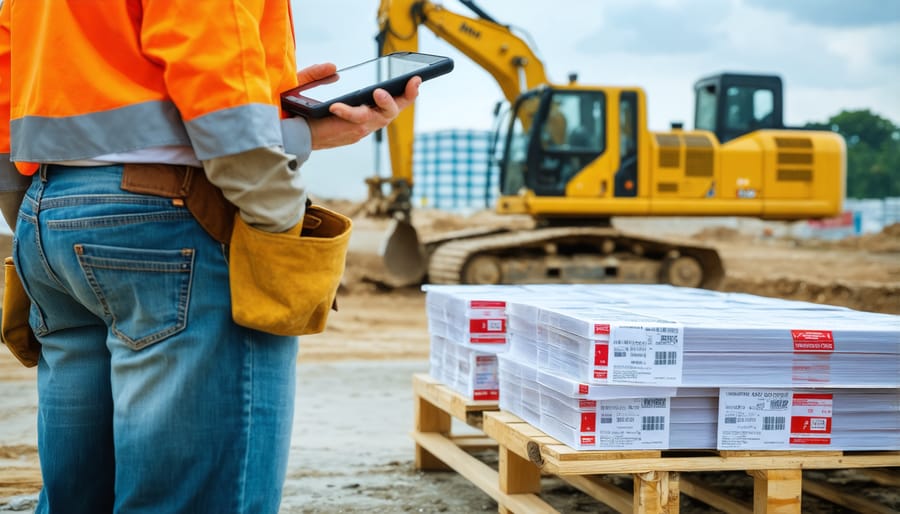
Data Collection and Analysis
Modern electronic inventory management systems leverage IoT sensors and advanced data collection methods to transform raw data into actionable business intelligence. These digital construction tools utilize RFID tags, QR codes, and wireless sensors to continuously monitor inventory levels, location, and movement in real-time.
The data collection process begins with strategically placed sensors that track key metrics such as quantity, temperature, humidity, and spatial positioning. These sensors transmit information to central databases through secure wireless networks, where sophisticated algorithms process and analyze the incoming data streams.
Machine learning algorithms identify patterns, predict demand fluctuations, and flag potential supply chain disruptions before they impact operations. The system automatically generates detailed reports on inventory turnover rates, storage optimization opportunities, and procurement timing recommendations.
Real-time analytics dashboards provide construction managers with vital insights through customizable visualizations and automated alerts. This enables quick decision-making regarding reorder points, stock rotation, and resource allocation. The system can also integrate with enterprise resource planning (ERP) software to create a comprehensive view of inventory operations across multiple project sites.
By analyzing historical data alongside current inventory movements, these systems can forecast future needs with increasing accuracy, helping construction firms maintain optimal stock levels while reducing carrying costs and preventing stockouts.
Implementation Benefits and ROI
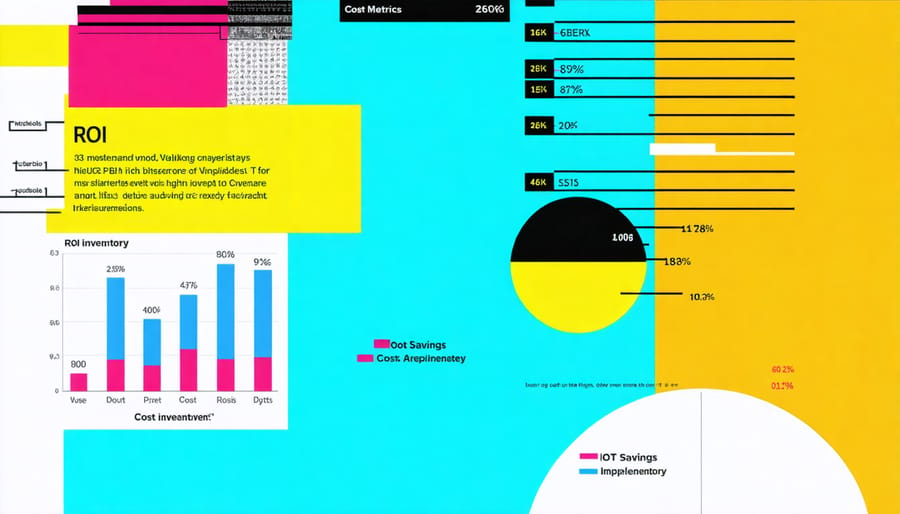
Cost Reduction and Efficiency Gains
Electronic inventory management systems deliver substantial cost reductions and efficiency improvements across multiple operational areas. Real-time tracking eliminates the need for manual stock counts, reducing labor costs by up to 30% and minimizing human error in inventory records. Construction firms implementing IoT-enabled inventory management report average carrying cost reductions of 20-25% through optimized stock levels and improved forecasting accuracy.
Automated reordering systems prevent costly stockouts while maintaining lean inventory levels, typically reducing excess stock by 15-20%. This optimization of storage space and working capital provides immediate financial benefits. The system’s ability to track tool and equipment usage patterns enables better maintenance scheduling, extending asset lifespan and reducing replacement costs by up to 25%.
Material waste reduction is another significant advantage, with smart inventory systems helping construction companies cut waste by 10-15% through better tracking of expiration dates and improved material rotation. Real-time visibility into material locations reduces time spent searching for items, with field teams reporting 40-50% less time spent on inventory-related tasks.
The integration of RFID tags and IoT sensors also streamlines receiving and dispatch processes, reducing processing time by up to 60% compared to manual methods. This efficiency gain translates to lower labor costs and improved project timelines. Additionally, automated documentation and reporting capabilities reduce administrative overhead while improving accuracy in compliance and audit processes.
Project Timeline Optimization
Electronic inventory management significantly impacts project timelines by streamlining material tracking and resource allocation processes. Construction firms implementing these systems report an average 23% reduction in project delays related to material availability issues. Real-time inventory tracking enables project managers to anticipate material needs and coordinate deliveries precisely, preventing costly schedule disruptions.
The system’s predictive analytics capabilities help optimize delivery schedules by analyzing historical data patterns and current consumption rates. This proactive approach allows construction teams to maintain optimal inventory levels while reducing storage costs and minimizing the risk of stockouts. Project managers can now make data-driven decisions about material ordering and allocation across multiple job sites.
Case studies from major construction projects demonstrate that automated inventory tracking systems reduce the time spent on manual inventory counts by up to 85%. This efficiency gain translates directly to improved project scheduling accuracy and faster completion times. The technology also enables better coordination between suppliers, contractors, and site managers through automated notifications and real-time status updates.
Integration with project management software further enhances timeline optimization by creating a seamless flow of information between inventory systems and project schedules. This connectivity allows for automatic schedule adjustments based on material availability and delivery times, ensuring that resource constraints are properly factored into project timelines. Construction firms can now deliver projects more reliably while maintaining better control over costs and resources.
Case Study: IoT Implementation Success
Robertson Construction, a mid-sized commercial construction firm based in Denver, Colorado, successfully implemented an IoT-based inventory management system across their operations in 2021, resulting in a 32% reduction in material wastage and a 45% improvement in project delivery times.
The company faced significant challenges with their traditional inventory management methods, including frequent stockouts, over-ordering of materials, and inefficient tracking across multiple job sites. These issues led to project delays and increased operational costs, prompting the search for a technology-driven solution.
Working with technology partner SmartSite Solutions, Robertson implemented a comprehensive IoT system featuring:
– RFID-enabled material tracking
– Smart sensors for monitoring storage conditions
– Automated reordering systems
– Real-time inventory visibility across all sites
– Mobile application integration for field teams
The implementation process spanned four months, beginning with a pilot program at two construction sites before expanding company-wide. Key to the success was a structured training program that ensured all site managers and procurement staff were comfortable with the new technology.
The results after 18 months of implementation were significant:
– Material waste reduction of 32%
– 45% improvement in project delivery times
– 28% decrease in emergency material orders
– 95% accuracy in inventory counts
– 40% reduction in time spent on inventory management tasks
Project Manager Sarah Martinez notes, “The system’s ability to automatically track material movement and predict usage patterns has transformed our operations. We now make data-driven decisions about procurement and storage, which has significantly reduced our carrying costs.”
One particularly innovative aspect was the integration of weather sensors with material storage monitoring. This feature helped prevent material damage by alerting site managers to potential weather-related risks, resulting in a 60% reduction in weather-related material losses.
The success of this implementation has led Robertson Construction to expand their IoT infrastructure to include equipment tracking and preventive maintenance scheduling, further optimizing their construction operations and resource utilization.
Critical success factors included:
– Phased implementation approach
– Comprehensive staff training
– Regular system optimization based on user feedback
– Strong support from senior management
– Integration with existing project management systems
Future-Proofing Construction Inventory Management
The construction industry is rapidly evolving towards more sophisticated inventory management solutions, with IoT technology leading the charge. Advanced sensors, artificial intelligence, and blockchain-enabled supply chain solutions are converging to create unprecedented visibility and control over construction materials and equipment.
Industry experts predict that by 2025, smart inventory systems will incorporate predictive analytics capable of forecasting material needs weeks in advance, significantly reducing costly delays and overstock situations. Real-time location systems (RTLS) are becoming more precise, with new ultra-wideband technology offering centimeter-level accuracy in tracking materials across vast construction sites.
Emerging trends include the integration of autonomous drones for inventory counting, AI-powered image recognition for automatic material identification, and smart contracts for automated procurement. These technologies are being enhanced by edge computing capabilities, allowing for faster processing and reduced latency in inventory decisions.
Construction firms are also exploring digital twin technology to create virtual representations of their inventory systems, enabling better visualization and optimization of material flow. This integration with Building Information Modeling (BIM) systems provides a comprehensive approach to resource management throughout the project lifecycle.
To remain competitive, construction companies should begin implementing scalable IoT infrastructure that can accommodate these emerging technologies while maintaining flexibility for future innovations.
Electronic inventory management represents a crucial advancement for modern construction operations. By implementing digital tracking systems, companies can significantly reduce waste, improve efficiency, and maintain better control over their resources. The key to successful implementation lies in careful planning, proper staff training, and selecting the right technology solutions for your specific needs.
To get started, assess your current inventory challenges and establish clear objectives. Next, evaluate various electronic inventory management systems based on your requirements and budget. Once selected, develop a phased implementation plan that includes comprehensive staff training and regular system performance reviews.
Remember that successful digital transformation is an ongoing process. Start with a pilot program in one area of operations, gather feedback, and make necessary adjustments before expanding. With proper planning and execution, electronic inventory management can deliver substantial returns on investment through improved productivity, reduced costs, and enhanced project delivery.