Supply chain management stands as the backbone of modern construction sector management, driving operational excellence and project success through five interconnected components. These fundamental elements – planning, sourcing, manufacturing, delivery, and returns – form a dynamic framework that determines how effectively organizations manage resources, control costs, and deliver value. In today’s complex construction landscape, where global pressures and digital transformation reshape traditional practices, mastering these core components has become increasingly critical for competitive advantage. Understanding their interplay enables construction professionals to optimize operations, reduce waste, and create resilient supply networks that can adapt to market volatility and evolving client demands. This comprehensive exploration delves into each component’s role, practical applications, and strategic importance in modern construction supply chain management.
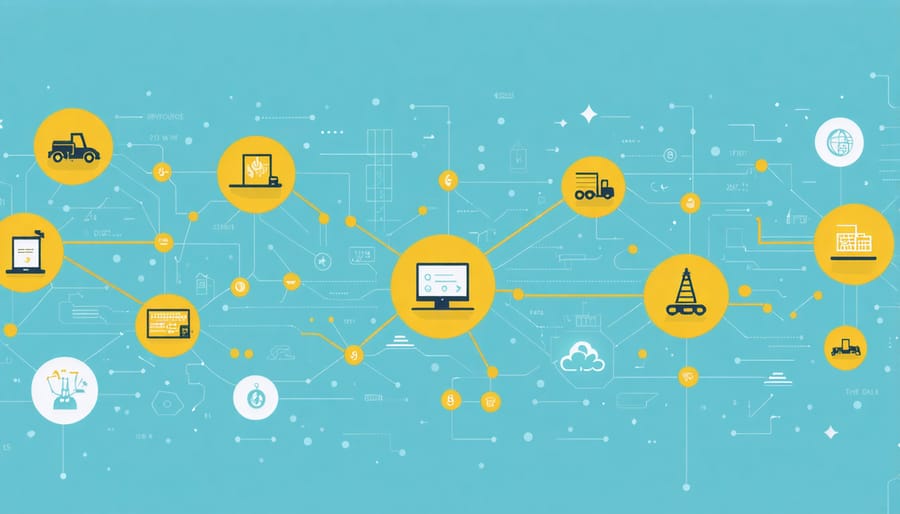
Strategic Planning and Demand Forecasting
Construction Demand Analysis
Construction demand analysis involves systematic forecasting of material and resource requirements through multiple data-driven methods. Historical project data analysis, coupled with advanced forecasting algorithms, enables accurate prediction of construction material needs across different project phases. Project managers typically employ a combination of quantitative methods, including moving averages and regression analysis, alongside qualitative assessments from experienced team members.
Key factors considered in demand analysis include seasonal variations, market trends, project timelines, and regional economic indicators. Building Information Modeling (BIM) technology has revolutionized this process by providing precise material quantity takeoffs and resource allocation predictions. Real-time data analytics tools further enhance accuracy by monitoring material consumption patterns and identifying potential supply chain bottlenecks.
Effective demand analysis also incorporates risk assessment factors, such as potential material price fluctuations, supplier reliability, and lead time variations. This comprehensive approach ensures optimal inventory levels while minimizing waste and maintaining project momentum through strategic resource allocation.
Risk Assessment and Mitigation
In construction supply chain management, effective risk assessment and mitigation are crucial for project success. Key strategies include maintaining buffer inventory for critical materials, developing relationships with multiple suppliers, and implementing real-time monitoring systems for supply chain disruptions. Construction managers must regularly assess potential risks such as material shortages, price fluctuations, and delivery delays, creating contingency plans for each scenario.
Digital technologies play a vital role in risk management, with predictive analytics helping identify potential bottlenecks before they occur. Regular supplier audits and performance evaluations ensure reliability and quality standards are maintained. Companies should also consider geographical diversification of suppliers to minimize regional disruption risks.
Financial risk mitigation involves strategic contract negotiations, insurance coverage, and careful cash flow management. Environmental and regulatory compliance risks require continuous monitoring and updates to supply chain processes, ensuring all partners meet current standards and certifications.
Procurement and Supplier Management
Vendor Selection Criteria
Selecting the right vendors is crucial for maintaining a robust supply chain in construction projects. Key criteria include financial stability, quality control measures, and proven track record of reliable deliveries. Vendors should demonstrate expertise in construction materials and showcase their ability to handle large-scale projects while maintaining consistent quality standards. Price competitiveness matters, but it shouldn’t overshadow other critical factors like technical capabilities and commitment to modular construction efficiency. Evaluate potential suppliers based on their compliance with industry regulations, safety standards, and environmental policies. Consider their geographical location, production capacity, and ability to scale operations during peak demands. Additionally, assess their technological infrastructure, communication systems, and willingness to forge long-term partnerships. Regular vendor performance reviews and maintaining strong relationships help ensure continuous improvement and mutual growth.
Contract Management
Contract management in supply chain operations involves strategic negotiation and maintenance of supplier agreements to ensure optimal project outcomes. Successful construction firms implement structured approaches to contract creation, including detailed scope definitions, performance metrics, and risk allocation frameworks. Key elements include clearly defined payment terms, delivery schedules, quality standards, and dispute resolution procedures.
Best practices emphasize the importance of establishing comprehensive service level agreements (SLAs) that protect both parties while fostering collaborative relationships. This includes incorporating mechanisms for price adjustments, change orders, and performance incentives. Regular contract reviews and updates ensure alignment with evolving project requirements and industry standards.
Effective contract management also requires robust monitoring systems to track supplier compliance and performance. Construction companies should maintain detailed documentation of all contract-related communications and implement systematic approaches to contract administration, including regular audits and performance evaluations. This proactive approach helps minimize disputes and ensures smooth project execution while maintaining positive supplier relationships.
Operations and Manufacturing
Production Planning
Production planning in construction supply chain management involves coordinating manufacturing processes, resource allocation, and project schedules to ensure efficient delivery of construction materials and services. This component focuses on optimizing production capacity, managing lead times, and synchronizing various stakeholder activities throughout the construction lifecycle.
Effective production planning requires detailed analysis of project requirements, resource availability, and timeline constraints. Construction managers must balance multiple factors, including material fabrication schedules, labor availability, equipment utilization, and site logistics. This coordination ensures that materials arrive at the construction site exactly when needed, reducing storage costs and minimizing waste.
Key aspects include capacity planning, workflow optimization, and schedule integration across suppliers, manufacturers, and construction teams. Advanced planning tools and methodologies, such as Last Planner System and Pull Planning, help streamline production processes and maintain project momentum while adapting to changes in demand or site conditions.
Quality Control
Quality control in supply chain management encompasses rigorous standards and procedures to ensure consistent product excellence throughout the entire supply chain network. In construction, this involves systematic inspection protocols at multiple checkpoints, from material sourcing to final installation. Key quality control measures include material testing, dimensional verification, and performance assessment against specified requirements.
Successful implementation requires detailed documentation systems, regular supplier audits, and comprehensive training programs for quality assurance personnel. Construction firms typically employ certified quality control managers who oversee compliance with industry standards such as ISO 9001 and project-specific requirements.
Real-time monitoring systems and digital quality management tools enable swift identification and resolution of potential issues before they impact project timelines. This proactive approach includes tracking key performance indicators (KPIs), conducting regular quality reviews, and maintaining detailed inspection records. By establishing clear quality benchmarks and maintaining strict adherence to specifications, organizations can significantly reduce rework costs and enhance project outcomes.

Logistics and Distribution
Transportation Management
Transportation Management in construction supply chains focuses on optimizing delivery systems and logistics to ensure materials, equipment, and resources reach project sites efficiently and cost-effectively. Modern construction technology innovations have revolutionized route planning and fleet management through GPS tracking and real-time analytics. Project managers utilize sophisticated software to coordinate deliveries, minimize fuel consumption, and reduce transportation costs while maintaining tight construction schedules.
Effective transportation management incorporates multiple delivery modes, including trucks, rail, and specialized heavy equipment transport, depending on project requirements and site accessibility. Load optimization and consolidation strategies help reduce the number of trips required, leading to decreased environmental impact and improved cost efficiency. Real-time visibility of shipments enables project teams to anticipate delays, adjust schedules proactively, and maintain continuous workflow on construction sites. This component also ensures compliance with transportation regulations, weight restrictions, and safety requirements specific to construction materials handling.
Inventory Control
Inventory control in construction supply chain management focuses on optimizing stock levels while minimizing holding costs and preventing stockouts. Effective warehouse management systems track materials, equipment, and supplies through real-time monitoring and automated reordering processes. Construction firms implement strategic buffer stock levels for critical materials to maintain project continuity while utilizing just-in-time delivery for bulk items to reduce storage costs.
Modern inventory management incorporates IoT sensors and RFID technology to monitor stock movements and conditions automatically. These systems integrate with project scheduling software to forecast material requirements and optimize procurement timing. Successful inventory control also requires careful consideration of storage conditions, particularly for temperature-sensitive materials and specialized equipment.
Best practices include implementing cycle counting procedures, maintaining accurate inventory records, and establishing clear protocols for material receipt and distribution. This systematic approach ensures materials are available when needed while minimizing waste and preventing project delays due to stock shortages.
Information Systems Integration
Digital Tools and Software
Modern supply chain management relies heavily on digital solutions to enhance visibility and control. Enterprise Resource Planning (ERP) systems serve as the backbone, integrating various operations and providing real-time data access. Construction-specific software like BIM (Building Information Modeling) platforms facilitate material tracking and resource allocation across project sites. Advanced analytics tools help forecast demand patterns and optimize inventory levels, while IoT sensors enable real-time monitoring of materials and equipment movement. Cloud-based supply chain management platforms offer collaborative features, allowing seamless communication between suppliers, contractors, and project managers. Mobile applications support field operations by providing instant access to inventory data and delivery status updates. Blockchain technology is emerging as a powerful tool for maintaining transparent supplier relationships and verifying material authenticity. These digital solutions collectively enhance decision-making capabilities and operational efficiency throughout the supply chain network.
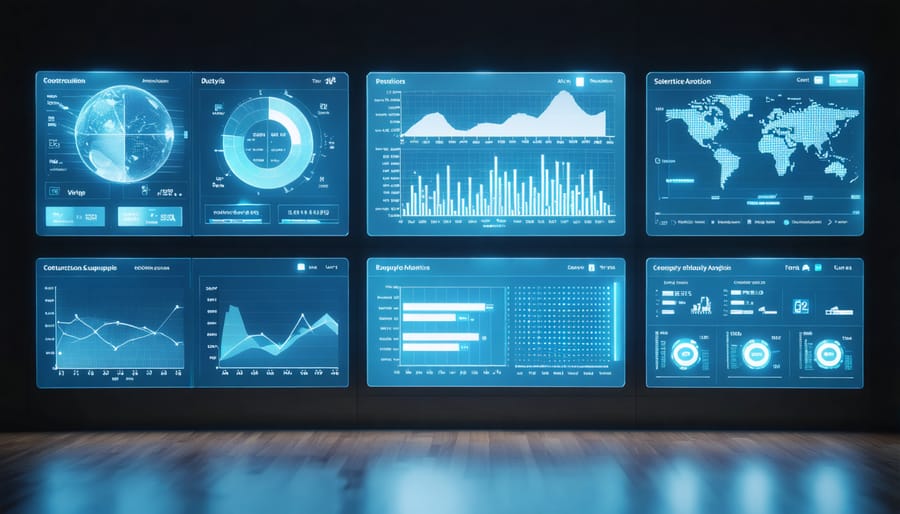
Data Analytics
Data analytics serves as the backbone of modern supply chain management in construction, enabling organizations to make informed decisions through real-time insights and predictive modeling. By analyzing historical data, market trends, and performance metrics, construction firms can optimize inventory levels, reduce waste, and improve project delivery timelines.
Key performance indicators (KPIs) such as lead times, supplier reliability scores, and materials utilization rates provide valuable insights for strategic planning. Advanced analytics tools help identify potential bottlenecks, forecast demand patterns, and streamline procurement processes. Construction companies increasingly utilize data visualization dashboards to monitor supply chain performance and make quick, informed decisions.
The integration of IoT sensors and real-time tracking systems further enhances data collection capabilities, allowing for precise monitoring of materials movement, equipment utilization, and site logistics. This data-driven approach enables proactive risk management and helps maintain optimal inventory levels while reducing carrying costs and preventing project delays.
The five components of supply chain management in construction – planning, sourcing, manufacturing, delivery, and returns – form an intricate web of interdependent processes that directly impact project success. When these elements work in harmony, they create a robust framework that enables efficient resource allocation, cost optimization, and timely project completion. Construction professionals must recognize that strengthening one component inherently enhances the others, creating a multiplier effect that benefits the entire supply chain ecosystem. By maintaining focus on these fundamental components and their interconnections, organizations can build resilient supply chains that adapt to market changes, minimize disruptions, and consistently deliver value to stakeholders. Success in modern construction projects increasingly depends on mastering these essential elements and leveraging their synergistic relationships to achieve operational excellence.