The construction industry stands at a pivotal crossroads between sustaining traditional linear production models and embracing circular economy principles that could revolutionize how we build. While linear economies follow the “take-make-dispose” pathway that has dominated construction for centuries, circular economies reimagine waste as a resource, transforming our $11.5 trillion global construction sector through systematic material reuse and regenerative design.
Recent data reveals that construction generates 35% of global waste, with only 20% currently being recycled or repurposed. The circular economy model presents a compelling $4.5 trillion economic opportunity by 2030, offering construction professionals a framework to reduce waste, optimize resource utilization, and create sustainable value chains. From modular building systems that enable component reuse to digital material passports that track resources throughout their lifecycle, circular principles are reshaping construction methodologies worldwide.
This transformation demands a fundamental shift in how we approach project planning, material selection, and waste management. By understanding the stark contrasts between linear and circular models, construction leaders can make informed decisions that not only benefit their bottom line but also contribute to a more sustainable built environment. The following analysis examines these two economic models, their practical implications for construction, and actionable strategies for implementation.
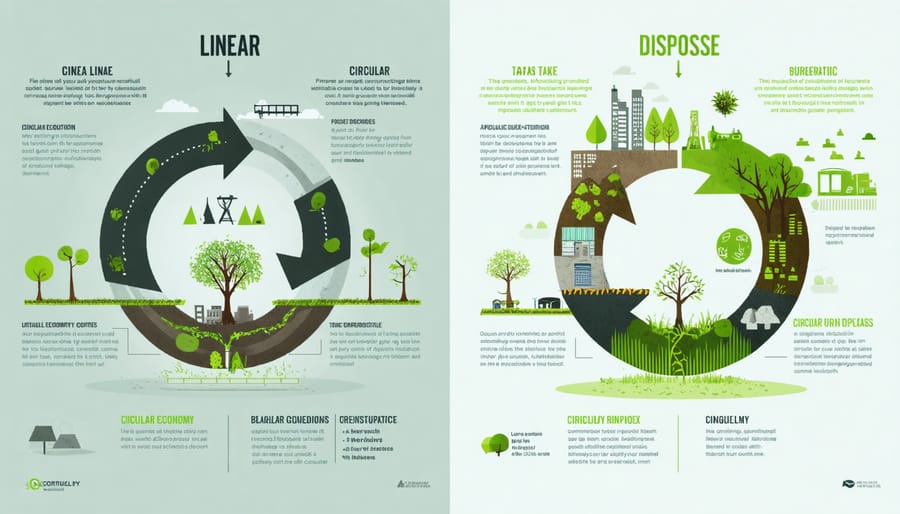
The True Cost of Linear Construction Economics
Resource Depletion and Rising Costs
The construction industry faces mounting challenges as traditional linear economic models continue to strain our planet’s finite resources. Global demand for construction materials is projected to double by 2060, driving unprecedented price volatility and supply chain disruptions. Recent market analyses show that key materials like copper, steel, and rare earth elements have seen price increases of 30-150% in the past decade alone. This scarcity isn’t just affecting bottom lines – it’s fundamentally threatening project viability.
Implementing effective resource management strategies has become crucial as virgin material costs continue to rise. Industry data indicates that companies following traditional linear models face 15-25% higher material costs compared to those adopting circular principles. The increasing scarcity of sand suitable for concrete production serves as a stark example, with prices rising by 40% in urban areas over the past five years.
These challenges are compelling construction firms to reevaluate their approach to resource utilization, particularly as regulations around material extraction become more stringent and disposal costs continue to climb. The economic imperative for change has never been clearer.
Waste Management Challenges
Construction companies face mounting challenges in waste management in construction, particularly under the traditional linear economy model. Current disposal costs average $50-100 per ton for construction waste, with landfill fees continuing to rise annually across major metropolitan areas. Regulatory compliance adds another layer of complexity, with strict requirements for hazardous material handling and documentation of waste streams.
Environmental regulations increasingly mandate specific disposal methods for different materials, requiring construction firms to implement sophisticated sorting and tracking systems. Many jurisdictions now require detailed waste management plans before issuing building permits, while others impose hefty fines for improper disposal practices.
The financial impact extends beyond direct disposal costs. Transportation expenses, labor costs for waste handling, and storage space requirements on constrained urban sites all contribute to the total waste management burden. Additionally, new Extended Producer Responsibility (EPR) regulations in some regions are shifting more disposal costs back to construction companies, making traditional linear waste disposal models increasingly unsustainable from both an environmental and economic perspective.
Circular Economy: The New Urban Construction Paradigm
Design for Disassembly
Design for Disassembly (DfD) represents a revolutionary approach in modern construction that aligns perfectly with circular economy principles. This methodology involves creating buildings and structures that can be efficiently deconstructed at the end of their lifecycle, allowing materials and components to be recovered, reused, or recycled effectively.
Key architectural strategies include the use of mechanical connections instead of adhesives, standardized components, and accessible joining systems. For instance, the Edge Olympic building in Amsterdam demonstrates these principles through its modular facade system and reversible connections, enabling future adaptability and material recovery.
Implementation requires careful consideration during the design phase, incorporating elements such as:
– Exposed connections for easy access
– Minimal composite materials
– Standardized and documented assembly sequences
– Clear material labeling and tracking systems
– Reversible joining methods
Leading architects and engineers report that DfD can reduce demolition waste by up to 95% while potentially decreasing construction costs by 10% through planned material recovery. The Dutch government’s CircularIQ office building exemplifies this approach, featuring demountable steel structures and mechanical fixings that allow for complete disassembly and material reuse.
By incorporating DfD principles, construction professionals can significantly enhance a project’s sustainability credentials while creating valuable material banks for future use. This approach represents a crucial shift from traditional linear construction methods toward a more sustainable, circular building industry.
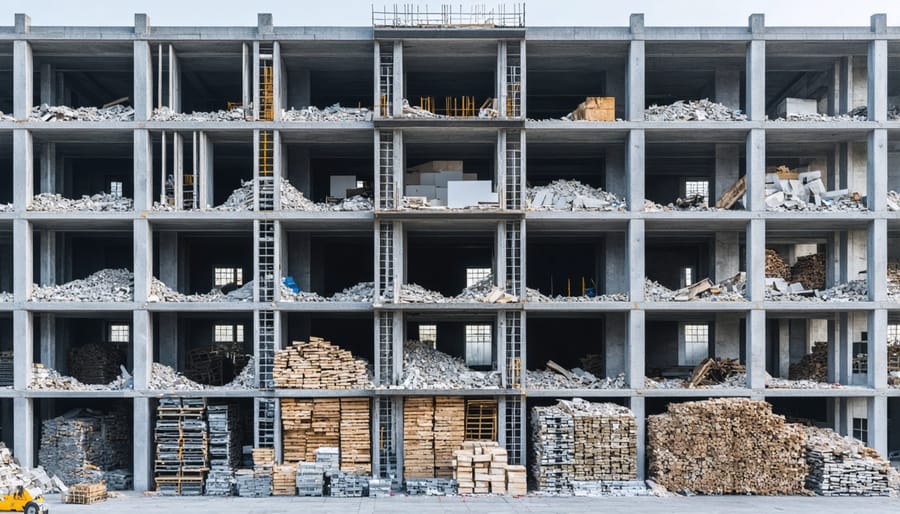
Material Passport Systems
Material passport systems represent a groundbreaking approach to tracking and managing construction materials throughout their lifecycle. These digital platforms create detailed documentation of building components, capturing essential information about material composition, location, quantity, and quality. This comprehensive data enables efficient recovery and reuse of materials when buildings reach their end of life, transforming them from waste into valuable resources.
The system works by creating a digital twin of the building, where each component is tagged and tracked with detailed specifications, maintenance history, and potential future applications. This information becomes invaluable during renovation or demolition phases, as it provides precise data about which materials can be salvaged and repurposed, their current condition, and optimal recovery methods.
Leading construction firms have reported up to 30% reduction in material waste through the implementation of material passport systems. For example, the Circl pavilion in Amsterdam demonstrated how material passports enabled the recovery and reuse of 95% of its building materials during construction.
These digital systems also facilitate compliance with emerging circular economy regulations and certification requirements. They provide transparent documentation of material sources and composition, supporting both environmental reporting and future material recovery planning. For building owners and developers, material passports create additional value by documenting the inherent worth of installed materials and enabling more accurate asset valuation based on future recovery potential.
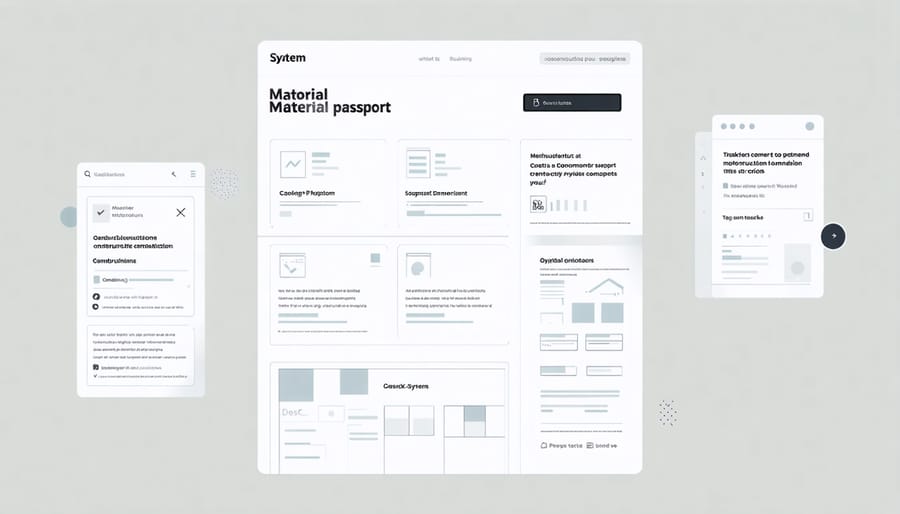
Reverse Logistics in Construction
In the transition from linear to circular construction practices, reverse logistics plays a crucial role in material recovery and reprocessing. This systematic approach involves collecting, sorting, and processing used building materials for reintegration into new construction projects. Advanced material tracking systems, utilizing RFID technology and digital documentation, enable efficient identification and categorization of recoverable resources throughout the demolition process.
Construction companies are implementing specialized recovery protocols that begin with pre-demolition audits to assess material value and recyclability. These audits typically identify high-value materials such as structural steel, copper wiring, and architectural elements that can be extracted with minimal degradation. Modern processing facilities employ automated sorting systems and quality control measures to ensure recovered materials meet industry standards for reuse.
The success of reverse logistics in construction depends heavily on establishing reliable collection networks and processing infrastructure. Leading construction firms have developed partnerships with specialized recycling facilities and material banks, creating efficient channels for material recovery and redistribution. These partnerships often utilize digital platforms to track material availability and facilitate transactions between demolition projects and new construction sites.
Cost-effective transportation and storage solutions are essential components of reverse logistics systems. Strategic placement of processing centers near urban construction hubs minimizes transportation costs while reducing carbon emissions. Companies are increasingly investing in modular storage solutions that protect recovered materials from degradation while awaiting reprocessing or reuse in new projects.
Real-World Success Stories
The Amsterdam Circle City Initiative
Amsterdam has emerged as a pioneering force in circular construction, implementing ambitious strategies to transform its built environment by 2050. The city’s comprehensive approach focuses on material reuse, waste reduction, and sustainable building practices across all construction projects.
The initiative has already achieved notable success through several key projects. In the Buiksloterham district, developers have incorporated 100% recyclable materials in new residential buildings, while implementing modular design principles that allow for future adaptation and dismantling. The city’s material passport system tracks construction resources throughout their lifecycle, enabling efficient reuse and recycling.
Construction companies operating within Amsterdam must now meet strict circular criteria, including a minimum of 30% recycled materials in new buildings and a requirement to design for future disassembly. This policy has driven innovation in construction methods and materials, with local firms developing new techniques for material recovery and reuse.
Notable achievements include the transformation of former office buildings into residential spaces using 90% existing materials, and the development of a circular concrete initiative that has reduced carbon emissions by 45% compared to traditional methods. The city’s material marketplace platform has facilitated the exchange of over 100,000 tons of recovered building materials since its launch.
Amsterdam’s success demonstrates that circular construction is not just environmentally beneficial but also economically viable, setting a replicable model for other cities worldwide.
London’s Circular Economy Building Standard
London has emerged as a global leader in circular construction with the introduction of its groundbreaking Circular Economy Building Standard in 2022. This comprehensive framework requires all major construction projects to submit a Circular Economy Statement, demonstrating how they will reduce waste, maximize resource efficiency, and extend building lifespans.
The standard mandates several key requirements: a minimum of 20% recycled content in construction materials, detailed end-of-life planning for building components, and design strategies that facilitate future adaptability and disassembly. Projects must achieve specific targets for material reuse and demonstrate how they will minimize embodied carbon throughout the building’s lifecycle.
Notable features include the mandatory material passports system, which tracks and documents all materials used in construction, enabling future recovery and reuse. The standard also requires developers to conduct pre-demolition audits and establish clear waste reduction targets, typically aiming for at least 95% of construction waste to be diverted from landfills.
Implementation has already shown promising results, with pilot projects reporting up to 30% reduction in construction costs and 40% decrease in waste generation. Major developments like the Southbank Place renovation have successfully demonstrated compliance, incorporating over 50% recycled materials and designing for complete disassembly at end-of-life.
The standard has become a blueprint for other cities worldwide, highlighting how regulatory frameworks can effectively drive the transition from linear to circular construction practices.
Implementation Strategies for Construction Companies
Assessment and Planning
Transitioning from a linear to a circular economy requires a systematic assessment of current practices and careful planning. Organizations should begin by conducting a comprehensive audit of their material flows, waste generation patterns, and resource consumption. This evaluation should identify areas where circular principles can be integrated with existing sustainable construction practices.
Key assessment steps include:
– Analyzing current material procurement and disposal processes
– Evaluating existing supply chain partnerships
– Identifying potential areas for material recovery and reuse
– Assessing the feasibility of implementing circular design principles
– Measuring current carbon footprint and waste metrics
Once baseline data is collected, organizations should develop a phased transition plan that includes:
1. Setting specific, measurable targets for waste reduction and resource recovery
2. Establishing timeline milestones for implementation
3. Identifying necessary technological investments
4. Planning staff training and development programs
5. Creating monitoring and reporting frameworks
The transition plan should incorporate both short-term quick wins and long-term strategic objectives. It’s essential to engage stakeholders across all levels of the organization and establish clear communication channels. Regular review and adjustment of the plan ensure continuous improvement and adaptation to changing market conditions and technological advances.
Technology and Partnership Requirements
Successful implementation of circular economy principles in construction requires both advanced technological solutions and strong collaborative partnerships. Digital tools like Building Information Modeling (BIM) and material passport systems are essential for tracking and managing resources throughout their lifecycle. These technologies enable precise documentation of materials used in construction, their location, quantity, and potential for future reuse.
Smart sensors and IoT devices play a crucial role in monitoring building performance and material degradation, helping optimize maintenance schedules and extend asset lifespans. Material scanning and sorting technologies are vital for efficient recycling and recovery processes, ensuring maximum value retention from demolished structures.
Partnership frameworks must extend beyond traditional supply chains. Construction companies need to establish relationships with material suppliers, waste management facilities, recycling plants, and other stakeholders in the circular value chain. Industry collaboration platforms and material exchanges facilitate the sharing of resources and knowledge between projects.
Cloud-based marketplace solutions enable efficient trading of secondary materials and components, while blockchain technology ensures transparency and traceability in material sourcing and certification. Strategic partnerships with research institutions and technology providers help companies stay current with emerging circular solutions and best practices.
For successful implementation, organizations should invest in staff training and development to build internal expertise in circular technologies and processes. Regular assessment of technological capabilities and partnership effectiveness ensures continuous improvement in circular economy practices.
The transition from linear to circular economy practices in urban construction is no longer just an environmental aspiration but a business imperative. By embracing circular principles, construction firms can achieve up to 40% reduction in waste management costs while creating new revenue streams through material recovery and reuse. The benefits extend beyond financial gains to include enhanced brand reputation, improved regulatory compliance, and reduced carbon footprint. As cities continue to grow and resources become increasingly scarce, the construction industry must act swiftly to adopt circular practices. The evidence from successful implementations worldwide demonstrates that circular construction is not only feasible but profitable. The time to transform our building practices is now – the technology exists, the methodologies are proven, and the market demands it. Forward-thinking construction professionals who embrace this change will lead the industry into a more sustainable and prosperous future.